Como todos saben, o esterilizador é un recipiente a presión pechado, normalmente feito de aceiro inoxidable ou aceiro ao carbono. Na China, hai uns 2,3 millóns de recipientes a presión en servizo, entre os que destaca especialmente a corrosión metálica, que se converteu no principal obstáculo e modo de fallo que afecta o funcionamento estable a longo prazo dos recipientes a presión. Como tipo de recipiente a presión, non se pode ignorar a fabricación, o uso, o mantemento e a inspección do esterilizador. Debido ao complexo fenómeno e mecanismo de corrosión, as formas e características da corrosión metálica son diferentes baixo a influencia dos materiais, os factores ambientais e os estados de tensión. A continuación, afondaremos en varios fenómenos comúns de corrosión de recipientes a presión:
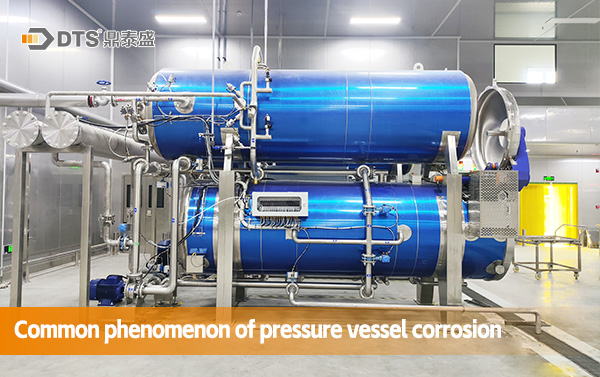
1. Corrosión integral (tamén coñecida como corrosión uniforme), que é un fenómeno causado pola corrosión química ou electroquímica, o medio corrosivo pode alcanzar todas as partes da superficie metálica de xeito uniforme, de xeito que a composición e organización do metal sexan condicións relativamente uniformes, toda a superficie metálica corróese a un ritmo similar. Para os recipientes a presión de aceiro inoxidable, nun ambiente corrosivo con baixo valor de pH, a película de pasivación pode perder o seu efecto protector debido á disolución e, a continuación, prodúcese corrosión integral. Tanto se se trata dunha corrosión integral causada por corrosión química como por corrosión electroquímica, a característica común é que é difícil formar unha película de pasivación protectora na superficie do material durante o proceso de corrosión, e os produtos de corrosión poden disolverse no medio ou formar un óxido poroso solto, o que intensifica o proceso de corrosión. Non se pode subestimar o dano da corrosión integral: en primeiro lugar, levará a unha redución na área de presión do elemento de soporte do recipiente a presión, o que pode causar fugas por perforación ou incluso rotura ou raspadura debido a unha resistencia insuficiente; En segundo lugar, no proceso de corrosión electroquímica integral, adoita ir acompañada dunha reacción de redución de H+, o que pode provocar que o material se encha con hidróxeno e, a continuación, quebra por hidróxeno e outros problemas, razón pola cal é necesario deshidroxenar o equipo durante o mantemento da soldadura.
2. A corrosión por picaduras é un fenómeno de corrosión local que comeza na superficie metálica e se expande internamente para formar un pequeno burato de corrosión en forma de burato. Nun medio ambiental específico, despois dun período de tempo, poden aparecer buratos gravados individuais ou picaduras na superficie metálica, e estes buratos gravados continuarán a desenvolverse en profundidade co tempo. Aínda que a perda de peso inicial do metal pode ser pequena, debido á rápida taxa de corrosión local, os equipos e as paredes das tubaxes adoitan estar perforados, o que provoca accidentes repentinos. É difícil inspeccionar a corrosión por picaduras porque o burato é de pequeno tamaño e adoita estar cuberto por produtos de corrosión, polo que é difícil medir e comparar cuantitativamente o grao de picaduras. Polo tanto, a corrosión por picaduras pode considerarse unha das formas de corrosión máis destrutivas e insidiosas.
3. A corrosión intergranular é un fenómeno de corrosión local que se produce ao longo ou preto do límite de gran, principalmente debido á diferenza entre a superficie do gran e a composición química interna, así como á existencia de impurezas no límite de gran ou tensión interna. Aínda que a corrosión intergranular pode non ser obvia a nivel macro, unha vez que se produce, a resistencia do material pérdese case instantaneamente, o que a miúdo leva á falla repentina do equipo sen previo aviso. Máis grave aínda, a corrosión intergranular transfórmase facilmente en fisuración por corrosión por tensión intergranular, que se converte na fonte de fisuración por corrosión por tensión.
4. A corrosión por fendas é o fenómeno de corrosión que se produce nunha fenda estreita (cuxo ancho adoita estar entre 0,02 e 0,1 mm) formada na superficie metálica debido a corpos estraños ou razóns estruturais. Estas fendas deben ser o suficientemente estreitas como para permitir que o fluído flúa e se detente, proporcionando así as condicións para que a fenda se corroa. En aplicacións prácticas, as unións de brida, as superficies de compactación de porcas, as unións de solape, as costuras de soldadura non soldadas, as gretas, os poros superficiais, a escoria de soldadura non limpa e depositada na superficie metálica da escala, as impurezas, etc., poden constituír fendas, o que resulta na corrosión das fendas. Esta forma de corrosión local é común e altamente destrutiva, e pode danar a integridade das conexións mecánicas e a estanquidade do equipo, o que pode provocar fallos do equipo e mesmo accidentes destrutivos. Polo tanto, a prevención e o control da corrosión por fendas son moi importantes, e requírese un mantemento e unha limpeza regulares do equipo.
5. A corrosión por tensión representa o 49 % do total de tipos de corrosión de todos os recipientes, e caracterízase polo efecto sinérxico da tensión direccional e o medio corrosivo, o que leva a fisuras fráxiles. Este tipo de fisura pode desenvolverse non só ao longo do límite do gran, senón tamén a través do propio gran. Co desenvolvemento profundo de fisuras no interior do metal, isto provocará unha diminución significativa da resistencia da estrutura metálica e mesmo danos repentinos no equipo metálico sen previo aviso. Polo tanto, a fisura inducida por corrosión por tensión (SCC) ten as características de ser destrutiva repentina e forte; unha vez que se forma a fisura, a súa velocidade de expansión é moi rápida e non hai un aviso significativo antes da falla, o que supón unha forma moi prexudicial de falla do equipo.
6. O último fenómeno común de corrosión é a corrosión por fatiga, que se refire ao proceso de dano gradual na superficie do material ata a súa rotura baixo a acción combinada da tensión alterna e o medio corrosivo. O efecto combinado da corrosión e a tensión alterna do material fai que o tempo de inicio e os tempos de ciclo das fisuras por fatiga se acurten obviamente, e que a velocidade de propagación das fisuras aumente, o que resulta nun límite de fatiga dos materiais metálicos moi reducido. Este fenómeno non só acelera a falla prematura do elemento de presión do equipo, senón que tamén fai que a vida útil do recipiente a presión deseñado segundo os criterios de fatiga sexa moito menor do esperado. No proceso de uso, para evitar diversos fenómenos de corrosión, como a corrosión por fatiga dos recipientes a presión de aceiro inoxidable, débense tomar as seguintes medidas: limpar a fondo cada 6 meses o interior do tanque de esterilización, o tanque de auga quente e outros equipos; se a dureza da auga é alta e o equipo se usa máis de 8 horas ao día, límprase cada 3 meses.
Data de publicación: 19 de novembro de 2024